Butelki plastikowe służą jako uniwersalny pojemnik na płyny. Mają przewagę nad pojemnikami szklanymi ze względu na swoją elastyczność i większą objętość. Plastikowe pojemniki po raz pierwszy pojawiły się w Stanach Zjednoczonych w 1970 roku i od tego czasu stały się szeroko rozpowszechnione na całym świecie.
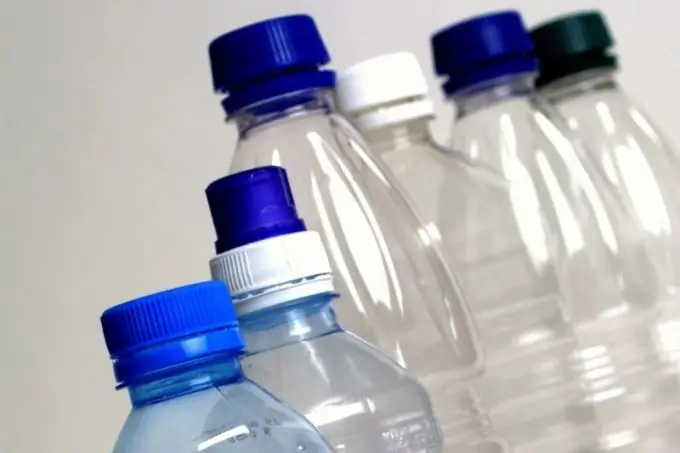
Instrukcje
Krok 1
Produkcja butelek plastikowych odbywa się na różne sposoby, które pozwalają osiągnąć wyższy stopień ochrony butelkowanego produktu. Są produkowane na specjalnym sprzęcie, a sama technologia produkcji nazywana jest „inflacją wewnętrzną”. Sam proces przebiega w dwóch etapach.
Krok 2
Najpierw wykonuje się specjalne preformy - półfabrykaty przypominające kształtem probówkę, posiadające szyjkę i miejsce do założenia specjalnego pierścienia. Próbki te są formowane przy użyciu specjalnego sprzętu składającego się z ogniw o różnych rozmiarach. Powstałe kolby są równomiernie podgrzewane w stacjach zanurzalnych. Następnie preformy umieszcza się w osobnych gniazdach na 10-15 minut, gdzie następuje dalsze ogrzewanie.
Krok 3
Po podgrzaniu próbki przechodzą dodatkowy etap przetwarzania zwany równoważeniem. W jego procesie temperatura jest rozprowadzana na powierzchni przedmiotu obrabianego, aby uniknąć pojawienia się deformacji podczas procesu wydmuchiwania. Jeśli równowaga jest zbyt krótka, ścianki butelki nie będą miały jednolitej grubości. Nadmierne ciepło może zdeformować szyjkę podczas dalszej obróbki. Podczas tej procedury preformy są podgrzewane do 100-110 stopni.
Krok 4
Następnie detale są dostarczane do sekcji wyjściowej za pomocą specjalnego urządzenia podającego, które monitoruje prawidłowe położenie detali w formach. Następnie produkt jest mocowany w maszynie i zaczyna się rozciągać w płaszczyźnie pionowej. Powietrze jest dostarczane przez szyjkę przyszłej butelki. Po ukształtowaniu obrabiany przedmiot jest chłodzony, dociskając do zimnych ścian formy i sztywnieje.
Krok 5
Plastikowe butelki po schłodzeniu lekko się kurczą, dzięki czemu temperatura przechowywania po produkcji jest stale monitorowana. Odbywa się to w celu zmniejszenia intensywności kompresji materiału w przyszłości, co pozwala na zmniejszenie do minimum różnicy między rozmiarami butelek uwalnianych w różnym czasie.